Rubber extrusion goes beyond just a manufacturing process. It is an art and science incorporated into one. In this blog, we’ll take you on an in-depth analysis into the world of rubber extrusion techniques, explaining each step in simple language while exploring its innovations, challenges, and wide-ranging applications. Whether you’re an industry veteran or a curious newcomer, you’ll find this guide both informative and engaging.
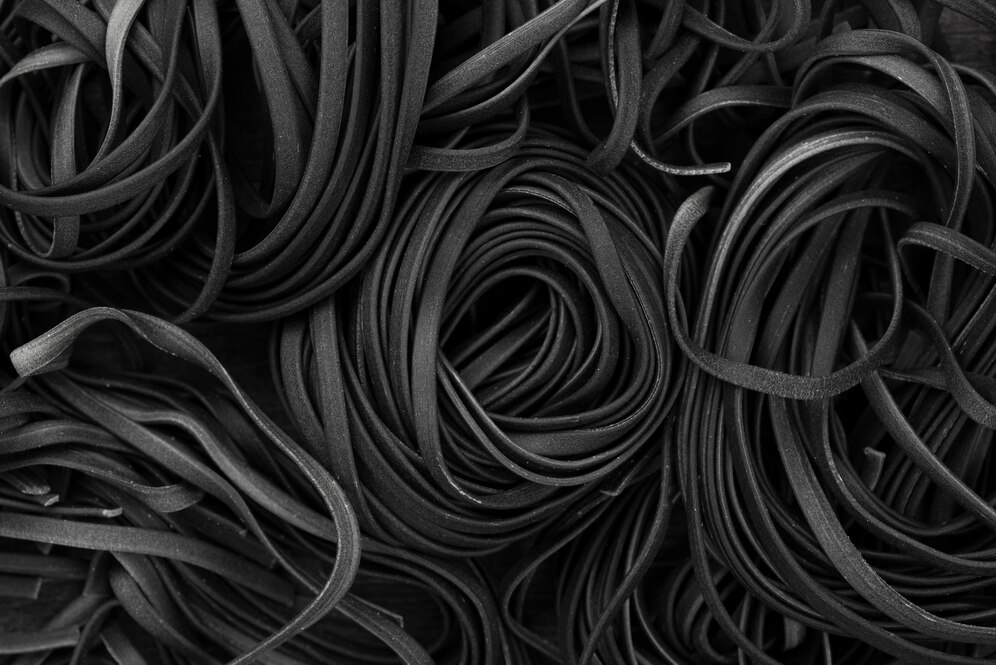
What is Rubber Extrusion?
At its basic, rubber extrusion is a manufacturing process where raw rubber compounds are forced through a specially designed die to produce continuous shapes with a consistent cross-section.
This process is crucial in creating a wide variety of rubber products, including seals, gaskets, hoses, and even the tires that keep our vehicles safely on the road. By controlling the shape and size of the extruded rubber, manufacturers can produce products that meet strict performance standards while also catering to innovative design needs.
The Science Behind the Process
Chemistry and Compounding
The magic of rubber extrusion begins long before the compound hits the extrusion machine. It all starts with selecting the right mix of natural or synthetic rubber, fillers, vulcanizing agents, and other additives. These ingredients are carefully combined to achieve the desired properties, whether it’s flexibility, durability, or resistance to high temperatures.
- Natural vs. Synthetic: Natural rubber offers excellent elasticity and resilience, while synthetic rubbers, like SBR (styrene-butadiene rubber) or EPDM (ethylene propylene diene monomer), are tailored for specific performance criteria.
- Additives and Fillers: Carbon black, silica, and other additives enhance strength and durability, while plasticizers and oils adjust flexibility.
Understanding the Extrusion Die
The extrusion die is the heart of the process. It’s designed with precision so that when the rubber compound is pushed through, it comes out in a consistent, pre-determined shape. The die can be customized to produce circular tubes, flat sheets, profiles, or even intricate custom designs.
Temperature, Pressure, and Flow
Temperature control is critical in rubber extrusion. Heating the compound makes it pliable enough to flow smoothly through the die, while the right pressure ensures that the material is evenly distributed. Maintaining optimal conditions is essential, as variations can lead to defects like voids, surface irregularities, or even premature wear of the die.
Step-by-Step: The Rubber Extrusion Process
1. Preparing the Rubber Compound
Before the extrusion begins, the rubber compound must be prepared with precision. This involves:
- Mixing: The raw rubber and additives are blended in mixers to create a homogeneous compound.
- Preconditioning: The mix is then heated to the right temperature to achieve the correct consistency. This preconditioning step ensures that the compound will flow smoothly during extrusion.
2. Feeding the Extruder
Once preconditioned, the compound is fed into the extruder—a machine that applies continuous pressure to push the rubber through the die. The extruder consists of:
- The Hopper: Where the compound is loaded.
- The Screw: A helical screw that pushes and mixes the material as it travels through the extruder barrel.
- The Barrel: A heated chamber that ensures the rubber stays at the ideal temperature.
3. Shaping Through the Die
As the compound moves through the extruder, it reaches the die, which shapes it into the desired profile. Here, precision engineering is paramount. The design of the die determines the final dimensions and surface quality of the extruded product.
4. Cooling and Vulcanization
After emerging from the die, the rubber shape must be cooled quickly to “set” its form. In many cases, the product then undergoes vulcanization—a chemical process where heat and pressure cause cross-linking between polymer chains, significantly enhancing the rubber’s strength and durability.
5. Finishing Touches
Once vulcanized, the extruded product may require further finishing processes. These can include:
- Cutting: Trimming the continuous product into specific lengths.
- Surface Treatment: Smoothing or texturing the surface as needed.
- Inspection: Quality control measures are implemented to ensure that every product meets stringent industry standards.
Innovations and Advanced Techniques
From Manual to Automated Systems
The world of rubber extrusion has evolved tremendously over the past few decades. In the early days, processes were manual and heavily reliant on the operator’s skill. Today, automation and computer-controlled systems have transformed the industry, ensuring consistency, precision, and efficiency.
Computer-Aided Design (CAD) and Simulation
Modern extrusion processes often incorporate CAD and simulation software. Engineers can design dies and predict flow behavior before production even begins, saving both time and materials. This innovation has led to fewer errors and more reliable production runs.
Process Control and Monitoring
Advancements in sensors and real-time monitoring have elevated quality control. Machines now continuously check temperature, pressure, and material flow, automatically adjusting settings to maintain optimal conditions. This level of control minimizes defects and enhances overall product quality.
Our Approach at Ambassador Industrial
At Ambassador Industrial, we pride ourselves on harnessing these innovations to deliver high-quality extruded rubber products. We continually invest in the latest technology and process control systems to ensure that every product leaving our facility meets rigorous performance standards. Our team of experts uses advanced simulation and real-time monitoring to optimize every batch, ensuring consistency and reliability without compromising on creativity or innovation.
Quality Control and Troubleshooting
Ensuring Consistency and Reliability
Quality control is a cornerstone of the rubber extrusion process. Manufacturers rely on strict protocols to ensure that every product meets quality standards. These measures include:
- Regular Inspection: Visual and instrumental inspections to detect any defects.
- Dimensional Checks: Measuring the extruded product to confirm that it matches design specifications.
- Material Testing: Analysing the rubber compound for consistency and performance characteristics.
Common Issues and How to Solve Them
Even with modern technology, issues can arise during extrusion. Some common challenges include:
- Die Swell: A phenomenon where the extruded rubber expands upon exiting the die. This can often be controlled by adjusting temperature and pressure.
- Surface Defects: Imperfections such as rough spots or streaks can occur due to contaminants or improper mixing. Regular cleaning and precise control of compound preparation are key.
- Inconsistent Flow: Variations in temperature or material composition can lead to uneven extrusion. Real-time monitoring and proper maintenance of equipment help mitigate this risk.
Learning from Experience
Each challenge in rubber extrusion is an opportunity to learn and improve. By understanding the underlying causes of defects and implementing rigorous quality control, manufacturers can continually refine their processes. This iterative approach not only improves product quality but also boosts overall efficiency.
Diverse Applications of Extruded Rubber
Automotive and Transportation
One of the most recognizable applications of rubber extrusion is in the automotive industry. Products such as hoses, seals, and gaskets are crucial for vehicle safety and performance. Rubber extrusion helps create components that can withstand extreme conditions, from high temperatures to constant vibration.
Industrial Machinery
In industrial settings, extruded rubber components play a vital role in ensuring smooth operations. They’re used in:
- Sealing Solutions: To prevent leaks in machinery and piping systems.
- Vibration Dampening: Helping to reduce noise and prolong the life of equipment.
- Protection: Coatings and bumpers that safeguard machinery from damage.
Construction and Infrastructure
Extruded rubber is also pivotal in construction. Whether it’s for weatherproof seals in windows and doors or vibration isolators in heavy machinery, the durability and flexibility of rubber make it an ideal material in the construction industry.
Consumer Goods
Beyond industrial applications, extruded rubber is found in everyday consumer products. From the soles of athletic shoes to various household items, the versatility of rubber ensures that it meets a diverse range of needs.
Looking Forward: The Future of Rubber Extrusion
Technological Trends
The future of rubber extrusion is bright and full of possibilities. Emerging trends are set to further revolutionize the industry:
- Smart Manufacturing: The integration of IoT (Internet of Things) devices and data analytics is leading to smarter, more responsive production lines.
- Advanced Materials: Research into new polymers and additives continues to push the boundaries of what rubber can do, making products more resilient, flexible, and sustainable.
- Customization: With increasing demand for personalized products, advances in extrusion technology allow for rapid adjustments to product design without sacrificing quality.
Overcoming Future Challenges
As technology advances, the rubber extrusion industry must continue to address challenges such as material variability and energy consumption. Ongoing research and development are key to refining processes, ensuring that innovations lead to tangible benefits in efficiency and product performance.
Embracing Change
Innovation is the lifeblood of any thriving industry. By embracing new technologies and sustainable practices, manufacturers can not only meet current market demands but also pave the way for future growth. The journey of rubber extrusion is far from over—if anything, it’s just beginning.
In Conclusion
Rubber extrusion techniques are at the forefront of modern manufacturing, blending traditional know-how with state-of-the-art technology. This process is a testament to the remarkable ways in which science and creativity converge to create products that are indispensable in our everyday lives. Whether it’s the robust seals in automotive engines or the flexible gaskets in industrial machinery, extruded rubber is a vital component that underpins safety, performance, and innovation.
By continually evolving our processes, embracing new technologies, and remaining committed to quality, we—alongside many industry pioneers—are shaping the future of rubber extrusion. This journey is not only about manufacturing; it’s about creating a legacy of excellence that will drive innovation for years to come.