Rubber extrusions are a key product for industries as they offer versatile and durable solutions for sealing, protection, and insulation. At Ambassador Industrial, we make sure that we deliver high-quality rubber extrusions that cater to the needs of our clients across different industries.
This blog will walk you through the details about rubber extrusions, what they are, their applications, and why they are essential in industrial settings.
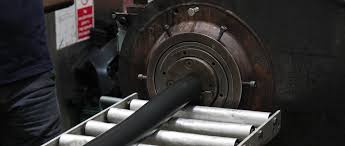
What are Rubber Extrusions?
Products that are formed by heating rubber compound material through a custom die to create a continuous shape or profile are called rubber extrusions. Depending on the specific requirements of the application they can be obtained in a wide range of shapes, and sizes which can be either natural or synthetic. Moreover, each offers you its unique properties that make them a perfect fit for various conditions and uses.
Rubber extrusions are mainly used in tasks which require sealing, insulation, vibration control, and protection. They are essential in industries like automotive, mining, construction, and marine where they help in maintaining the integrity and safety of systems and structures.
Types of Rubber Extrusions
Multiple types of rubber extensions are designed to serve specific functions which can cater to various industrial needs.
- Solid Rubber Extrusions: These dense and robust extrusions are used in applications requiring strong, durable seals or cushioning. They are ideally used in environments where the extrusion must be able to withstand high levels of pressure.
- Sponge Rubber Extrusions: These extrusions are cellular in structure which provides excellent compression and recovery properties. They are often used in applications where a softer and more flexible seal is essential, such as indoor or hatch seals or weather-stripping
- Dual Hardness Extrusions: This combines two different materials or hardness levels in a single extrusion and is used where durability is a crucial factor while the softer material may provide enhanced sealing.
- Speciality Extrusions: Custom-designed to meet specific requirements, these can be tailored according to your needs to include features like embedded metal reinforcements, unique shapes, or specific material properties to handle extreme conditions.
Benefits of Using Rubber Extrusions
These extrusions can offer you numerous advantages which make them a top-notch choice for a variety of industrial applications.
- Durability: Rubber extensions are widely known for their capability to withstand harsh conditions which also include extreme temperatures, chemicals, and UV exposure. This durability ensures a long life of your rubber extrusions even in challenging circumstances.
- Flexibility: The flexibility of the extrusions allows them to be manufactured in a wide variety of applications and can be easily moulded into different shapes and sizes, making them suitable for custom designs and for specific project needs
- Cost-effectiveness: Rubber extrusions are a cost-effective solution for many industries due to their longevity and low maintenance requirements. Their ability to cope with wear and tear reduces the need for frequent replacements which saves time and money in the long run for you.
- Versatility: With a wide variety of materials available, rubber extrusions are designed to meet the specific needs of different applications. Whether you are looking for resistance to chemicals or high temperatures or environmental exposure, these rubber extensions will meet all of your requirements.
- Ease of Installation: One of the most useful advantages of these rubber extrusions is that they are easy to install which cuts back on downtime and labour costs. Many extrusions are designed with features such as self-gripping edges or adhesive backing that simplify any further installation process.
Rubber Extrusions: Material Comparison Guide
While choosing the right material, it is important for you to ensure that the product meets the specific needs of your application. Different materials offer a variety of properties such as flexibility, durability, resistance to environmental factors, and temperature tolerance. Here is a guide to help you understand the types of rubber extrusions available and their properties.
Properties | EPDM (Ethylene Propylene Diene Monomer) | Neoprene (Polychloroprene) | Natural Rubber (NR) | Silicone Rubber (SR) | NBR Nitrile (Nitrile Butadiene Rubber) |
Temperature Range: | -40°C to +120°C | -40°C to +120°C | -50°C to +70°C | -60°C to +230°C | -30°C to +120°C |
Chemical Resistance: | Good, particularly for water-based chemicals | Moderate, particularly for oils and solvents | Limited | Moderate | Excellent, particularly for oils and fuels |
Abrasion Resistance: | Moderate | Good | Excellent | Moderate | Excellent |
Flexibility: | High | Moderate | High | High | Moderate |
Ozone & UV Resistance: | Excellent | Good | Poor | Excellent | Poor |
Compression Set: | Good | Moderate | Good | Excellent | Good |
Custom Rubber Extrusions at Ambassador Industrial
At Ambassador Industrial, we care about the needs of our clients and create our products keeping in mind the unique needs of our clients, which results in high-quality rubber extrusion profiles that can be customised to suit specific applications.
Therefore choosing the right material is necessary along with knowing which material would include various properties such as temperature range, chemical resistance, and flexibility.
To ensure optimal performance for your specific needs our team here at Ambassador Industrial is prepared with their bag full of solutions and the availability of high-quality products to assist you in selecting the ideal rubber extrusion to make your projects successful.
Conclusion
Understanding the types of rubber extrusions, their benefits, and how to choose the right material will help you make an informed decision with no room for any doubts. Their versatility and durability make them appropriate for a wide range of applications ranging from automotive and mining to construction and marine.
These extrusions are important to many industries for their capability to offer solutions for sealing, protection, and insulation. To gain more insights on rubber extrusions, you can go through our website and contact us if need be. Our dedicated team at Ambassador Industrial will assist you in finding the ideal rubber extrusion solution that aligns with your project’s requirements.
To talk to us you can call +61 3 97965588 or write to us at info@ambassindustrial.com.au.